Inventor, Designer, Engineer, Creator of wonderful things
Recent products
Lead design engineer on Marvel's - Groove N' Grow Groot!
​
Groove N' Grow Groot is just plain FUN! Originally I was asked the question... "Can we make a Groot to REALLY GROW!?" Of course, this had been attempted many times previously, both internally and externally by Hasbro, but nothing quite fit the bill. During the height of the pandemic, I found myself creating telescoping legs out of PVC and worm gears in my home office. Although the first breadboard was rather rough, it sold in the concept!

A fond farewell...
Groove n' Grow Groot was my last animatronic project before transitioning to the Nerf Brand team. Couldnt ask for a better send off!
Growing!
The original ask was to grow groot from his small 14 inches to a whopping 32 inches! This proved to be challenging as you could imagine, but we did it! Unfortunately, like most situations, cost is king and cost reductions had to shrink him, but we still ended with an amazing product!

​
The Nerf hit detection suit is a revolutionary addition to the Nerf sporting community. Partnering with an external company, we were able to modify their technology to "Suit" our needs!
Lead design engineer/Project manager on Nerf - Nerf Hit detection suit
I worked hand in hand with the design and marketing teams, who were tasked with creating an entirely new sport! We solicited feedback from the community and influencers in the Nerf community. Watching my suits work for the first time was truly magical!
Unfortunately, I must limit my description of the technology because of legal issues... You will just have to wait like everyone else!
​
Worked closely with the internal Star Wars brand team, and licensor to create a unique animatronic product. I led the mechanism design, the material exploration (ears), the gameplay design, and all firmware animation code.
Lead design engineer on Star Wars - The Mandalorian The Child animatronic edition
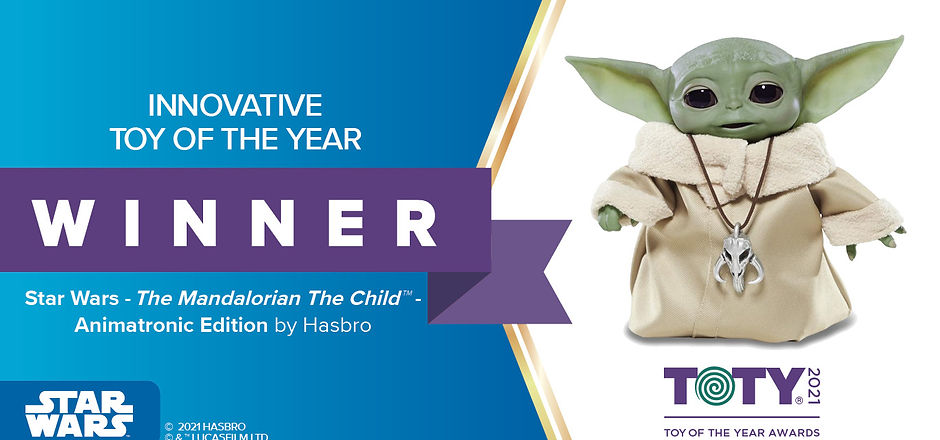
Sales samples
One fun and unique part of this project was to hand build the models for any and all internal sales events. These samples were also used for commercial shoots, box photography, etc. I was always off to the side with a control box, running the models.

(You can see me in the background a few times)
One of four samples I hand built, and programmed for the show. I am off to the left standing behind the wall!
Lead design engineer on Marvel's - Deadpool's Head
Worked hand in hand with the internal Marvel brand team, licensor and talented internal Hasbro designers to create a one of a kind animatronic product. I led the mechanism design, aided in production methods and fabric integration, led animation development, assisted in audio asset development, and UX gameplay and design for the app.
Too much fun!
This was by far, my favorite project! Being a huge Marvel / Deadpool fan, I couldn't resist giving this product my all! Late nights and weekends went into seemingly endless details for this product. Everything from the texture of the collar, to the fake blood stains on the bottom of the box (it is a severed head after all!).
Gameplay
Countless hours were spent, designing, testing and approving hundreds of audio assets and animations. Brainstorms for audio content, approvals from licensor, and sign off's from the brand teams were all part of the plan! All in all, this took about 6 months for full gameplay and animation development alone!

Once in a lifetime product
Many products are good, this one was great! Working closely with my good friend and co-worker Brian Torney, we were able to truly bring this once in a lifetime product to market!
4th wall breakage
Having hand built many of the samples seen in these video's, I have a very unique perspective! For example, one such model was so loved and revered by its audience, that he was literally hugged to DEATH!
(ie. someone squeezed it too hard and the SLA shell on his jaw snapped during an internal sales pitch)
Many more project's coming...
Stay Tuned!
Lead design engineer on the Joy for All - Companion Pets
These were originally "Furreal friends" pets, some of the first made, in fact. I led the team that updated gameplay, firmware, and added a few new tricks to achieve something unique!

The heart grows fonder
In both the cat, and the dog, one extra added feature was the use of a custom designed vibration speaker (The same speaker I engineered for Kreo- Sonic motion technology). With this addition, we were able to feel the cat purr, and feel the dog's heartbeat!
The split...
Based on its success, and the need for many dedicated resources for marketing, it was decided that the Joy for All brand would leave Hasbro and form its own company, Ageless innovation.
Finally
There are more news articles, user reviews and personal testimony's about this products success and impact, than one could count. I feel truly fortunately to have led this development, and very proud of its success!

To boldly go...
Never before had robotic pets been marketed to the elderly or their caregivers. It was quickly found, that by taking existing product, adding some new features and gameplay, that it would be widely successful!
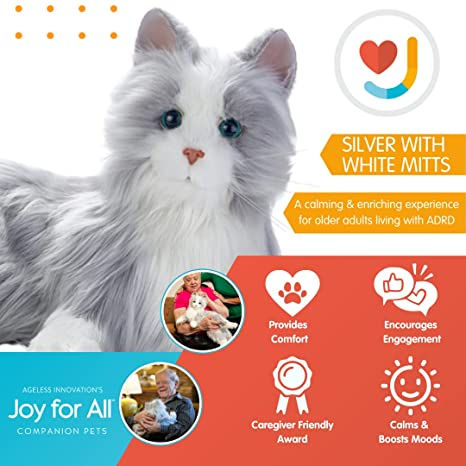
Lead design engineer on the Furreal Friends - Ricky the trick-lovin' pup
This one was definitely one of my more unique products. Looking like a regular furreal friends animatronic dog, you would never expect all that I packed in it! From feeding it treats (and consequently "releasing" them), to licking your face, this pup has it all!
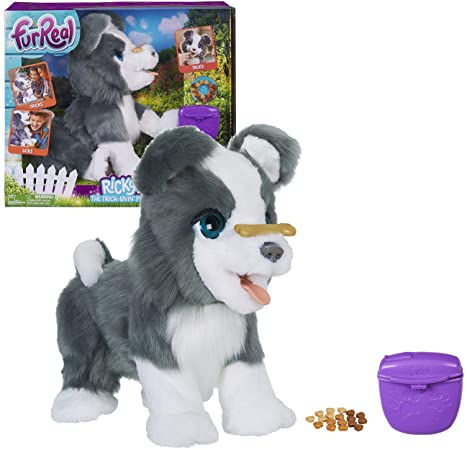
We need only balance
The challenge... create an animatronic dog that can perform tricks! Well, as you can imagine, many brainstorms about what these tricks are took place, and we ended up on...
"Can he balance a bone on his nose, then catch it!?"
~ internal marketer
My task... MAKE IT HAPPEN!
.jpg)
LET'S BREAK IT DOWN!
Aside from the normal "make him look alive" (ie. head, tail, eye, and ear movement). we needed to feed him, let him poop, stand, sit, balance and catch a bone, lick someone's face AND be fully interactive when you pet him! All this needed to be done, and with just 2 MOTORS!
​
Definitely one of my more challenging engineering executions; not simply from complexity, but from a cost standpoint as well!
Mechanism consultant - DJ Bumblebee
With most of my products, I am the design engineer; ie. I take the product from prototype to production, and have a say in every aspect of its development. This project, I was asked only to design a mechanism for production that is one motor, at target cost, and gets as much movement as possible.
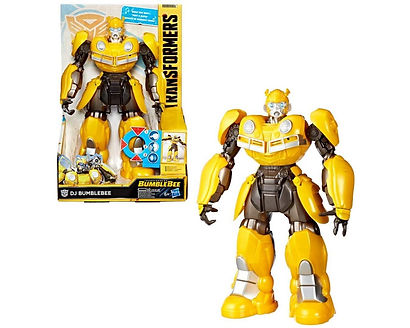
Cost is King!
Having a mechanism dance is actually a very simple thing! Doing it with a single DC motor, and very few parts is not! Like all products I work on, we are always looking to achieve what has never been done before. In this case, we have never got so much movement, playability and personality from so few parts and a single DC motor.
Aside from a DC motor, and a simple gearbox for torque, there is only 1 part in this product considered to be part of the "mechanism", the rest of the functionality comes from the internal design of the body shells.
Cost is still King
Unfortunately, because of costing issues, the gearbox is louder than I wanted, but as I said...
Cost is still king!
Mechanism consultant - MLP Giggles pinkie pie
Just like with DJ Bumblebee, I was asked for mechanism development only. As this was a low cost item, simplicity of the mechanism was key!
Materials
As the mechanism for this product was very straight forward, it became more of an exercise in material exploration for her body.

Mechanism consultant - Deer Pong
.jpg)
Just a quick one!
Just a quick prototype built and mechanism designed for production. Quick but still a fun one! I had never animated a deer's head hanging on the wall before!
Lead design engineer on the Baby Alive - Real As Can Be
From materials research to manufacturing methods, this project had it all! Turned out quick nice, if I do say so myself!

Create the most realistic baby doll...EVER!
"If it was easy, then anyone could do it", always the phrase said after a brand team kicked me off on a new project. How can we get the most emotive baby doll out there!? Using a 2 motor system, I was able to make her talk, smile, frown, close her eyes, turn her head and move her body!
Material exploration
Unfortunately, because of QA concerns regarding longevity of the flexible material on the face, we needed to proceed with a slightly stiffer face material in production.
​
The original spec'd out material (SEBS) was found to degrade too quickly and didn't pass our internal QA requirements for longevity. Also, as the Baby Alive brand is very popular in Latin America, we found that the SEBS material collected dirt and debris much faster than our final production material PVC.